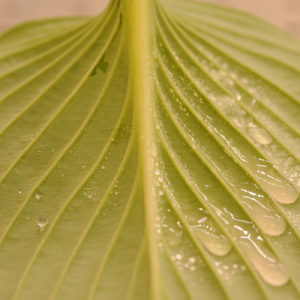
Drops of water bead up or roll right off the leaves of the lotus, making for that metaphysical metaphor – live like a lotus in the water. But the leaves of plants such as wheat, onion and cabbage are also water-repelling, or hydrophobic, and this can be a problem for farmers because pesticides sprayed on the leaves bounce off, leaving only a minuscule portion behind.
Professor Kripa Varanasi’s team at Massachusetts Institute of Technology has developed a new technology that has the potential to reduce the amount of pesticide that rebounds off the leaves of crops. Results in the lab indicate that this system could allow farmers to use only a tenth of the usual amount of pesticide to get the same effect they do now. This summer, the system, which promises to benefit both the environment and the farmer, is being tested on the ground.
Unlikely progression
Six years ago, the researchers at Varanasi’s lab had demonstrated the concept of a permanently wet slippery surface that would help liquid glide out of a container. Their five-second video of ketchup sliding out of a bottle down to the last drop went viral. Companies around the world began inquiring about the coating that made it possible. The same year, Varanasi co-founded LiquiGlide Inc, a company whose technology enables formulation of coatings for a range of applications – consumer packaged goods, manufacturing processes, medical devices and oil pipelines.
But agricultural sprays, such as pesticides, pose the opposite problem of condiments in a bottle – and so the scientists wanted to find a way to make the liquid stick.
Every year, some 5.6 billion pounds of pesticides are used worldwide. A bulk of these chemicals, up to 98%, eventually make their way into groundwater, lakes and rivers, hurting aquatic ecosystems. This is disastrous for the environment and a major loss for farmers worldwide, who annually spend roughly $100 billion on pesticides. “With our solution, there is a 10-fold reduction in lab scale, but assuming 50% (or two-fold reduction) at farm scale, we would still estimate savings in billions of dollars per year,” said Varanasi.
What does all this mean for the small farmer? Substantial savings. According to some estimates, they currently spend up to half the production cost on pesticides. Further, in developing countries, small farmers tend to spray crops without using protective gear because either they cannot afford it or they are unaware that exposure to pesticides can lead to certain nervous diseases, reproductive problems and cancer.
To minimise such costs to society, Varanasi considered this – can the surface of the leaf be altered so the pesticide sticks better? Farmers had already tried agents like surfactants, or soap-like chemicals, to lower the surface tension of the droplets and moisten the leaves better, but the results have been less than convincing. The bouncing off happens in a matter of tens of milliseconds, which is too short a time frame for the surfactant to be effective, Varanasi explained.
It was time for a new approach.
Bring opposites together
In 2013, MIT’s newly-formed Tata Center for Technology and Design, whose stated goal is “to bring rich technical talent and experience to bear on the persistent and emerging challenges in developing world countries”, funded Varanasi’s initiative. Along with his graduate student Maher Damak, he visited agricultural universities in Junagadh and Hyderabad. The farm visits were an eye-opener for the city-bred visitors.
“Depending on the crop, farmers deal with different bugs at different stages,” Varanasi said. “Even before the leaves start sprouting and right up to the harvest, they are up against something or the other.” The spraying must be relentless to match. How can pesticide usage possibly be lowered?
This time, Varanasi’s lab came up with a technology that was the very opposite of LiquiGlide, one whose goal was to transform droplets that tend to bounce off into sticking droplets. This could be achieved thanks to two different additives, both of which are non-toxic, biocompatible, and biodegradable.
Here is how it works: The pesticide is split into two portions and each gets a specific additive. One additive is a polymer which gives the solution a negative charge and the other gives it a positive charge. As the two solutions with opposite charges spread and meet on the surface of leaf, they create “pinning points” that help the pesticide stick better. This process increases the retention of pesticides up to ten-fold.
In 2016, when the paper which described the efficacy of the modified spray was published in Nature Communications, the popular press also publicised the discovery. Immediately, the group received calls and emails from crop growers on different continents, said Varanasi. This was like LiquiGlide story, Part Two.
Putting it to the test
Crop growers eager to reduce their pesticide footprint clamoured for field tests. The researchers had many potential candidates to choose from and three sites made the cut – a vineyard in Italy, a citrus grove in Florida, and a berry farm in Sharon, Massachusetts, a short drive away from the MIT campus. In the lab, the researchers ensured that that the additives did not harm the leaves in any way.
Starting this April, Varanasi and Damak have been visiting the chosen three farms to supervise the field trials. Already, there are encouraging reports that the pesticides are “spreading well”. Data collected at these sites will tell the researchers just how effective the additives have been. The feedback will help them refine their formulations for clients in the future.
The design of the spraying machine, which varies slightly in different countries, may also come in for some tweaking. In large mechanised farms, typically, tractors are fitted with nozzles to do the spraying. “Our goal is to make the delivery of pesticides as efficient as possible,” said Damak, who is now a post-doctoral researcher at MIT. “The retrofitting should be minimal, the usage seamless.”
Like LiquiGlide, this technology too is likely to be commercialized soon. This is the typical route innovation takes at top research universities like MIT these days – research paper and prototype for field testing, to product from a spin-off company.
Though the project has other sources of funding now, Tata Center’s initial funding got it off the ground. Later this year, the researchers will be testing their system in India – the details are yet to be finalised. This development should make Varanasi’s mother, who lives in Hyderabad, happy. When farmer suicides were constantly in the news in India, moved by their plight, she had asked her son once – “Can’t you do something about this problem?”
Finally, he seems to be taking steps in that direction with an innovation that might just benefit farmers not just in India, but the world over.
Read the article here. html.